- Market services
- Indigenous advisory
-
Compliance audits & reviews
Our audit team undertakes the complete range of audits required of Australian accounting laws to help you to help you meet obligations or fulfil best practice procedures.
-
Audit quality
We are fiercely dedicated to quality, use proven and globally tested audit methodologies, and invest in technology and innovation.
-
Financial reporting advisory
Our financial reporting advisory team helps you understand changes in accounting standards, develop strategies and communicate with your stakeholders.
-
Audit advisory
Grant Thornton’s audit advisory team works alongside our clients, providing a full range of reviews and audits required of your business.
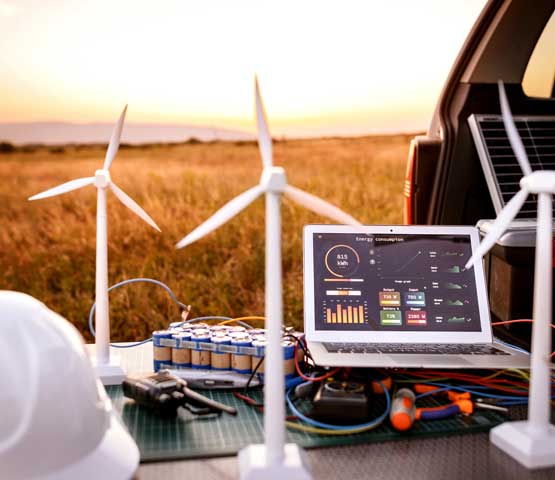
-
Corporate tax & advisory
We provide comprehensive corporate tax and advisory service across the full spectrum of the corporate tax process.
-
Private business tax & advisory
We work with private businesses and their leaders on all their business tax and advisory needs.
-
Tax compliance
We work alongside clients to manage all tax compliance needs and identify potential compliance or tax risk issues.
-
Employment tax
We help clients understand and address their employment tax obligations to ensure compliance and optimal tax positioning for their business and employees.
-
International tax
We understand what it means to manage tax issues across multiple jurisdictions, and create effective strategies to address complex challenges.
-
GST, stamp duty & indirect tax
Our deep technical knowledge and practical experience means we can help you manage and minimise the impact of GST and indirect tax, like stamp duty.
-
Tax law
Our team – which includes tax lawyers – helps you understand and implement regulatory requirements for your business.
-
Innovation Incentives
Our national team has extensive experience navigating all aspects of the government grants and research and development tax incentives.
-
Transfer pricing
Transfer pricing is one of the most challenging tax issues. We help clients with all their transfer pricing requirements.
-
Tax digital consulting
We analyse high-volume and unstructured data from multiple sources from our clients to give them actionable insights for complex business problems.
-
Corporate simplification
We provide corporate simplification and managed wind-down advice to help streamline and further improve your business.
-
Superannuation and SMSF
Increasingly, Australians are seeing the benefits, advantages and flexibility of taking control of their own superannuation and retirement planning.
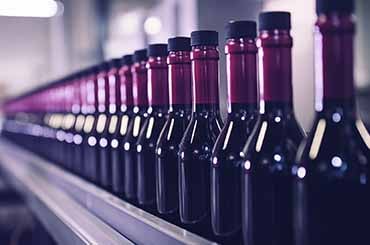
-
Payroll consulting & Award compliance
Many organisations are grappling with a myriad of employee agreements and obligations, resulting in a wide variety of payments to their people.
-
Cyber resilience
The spectrum of cyber risks and threats is now so significant that simply addressing cybersecurity on its own isn’t enough.
-
Internal audit
We provide independent oversight and review of your organisation's control environments to manage key risks, inform good decision-making and improve performance.
-
Financial crime
Our team helps clients navigate and meet their obligations to mitigate crime as well as develop and implement their risk management strategies.
-
Consumer Data Right
Consumer Data Right (CDR) aims to provide Australians with more control over how their data is used and disclosed.
-
Risk management
We enable our clients to achieve their strategic objectives, fulfil their purpose and live their values supported by effective and appropriate risk management.
-
Controls assurance
In Australia, as with other developed economies, regulatory and market expectations regarding corporate transparency continue to increase.
-
Governance
Through fit for purpose governance we enable our clients to make the appropriate decisions on a timely basis.
-
Regulatory compliance
We enable our clients to navigate and meet their regulatory and compliance obligations.
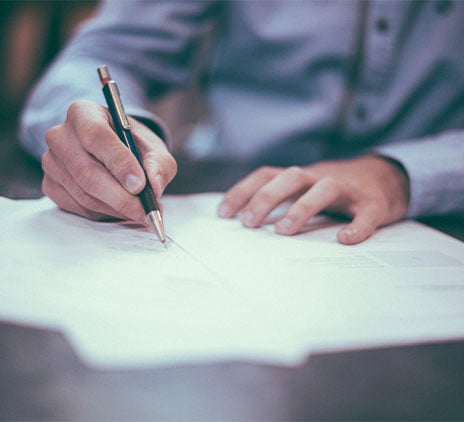
-
Forensic accounting and dispute advisory
Our team advises at all stages of a litigation dispute, taking an independent view while gathering and reviewing evidence and contributing to expert reports.
-
Investigations
Our licensed forensic investigators with domestic and international experience deliver high quality results in the jurisdictions in which you operate.
-
Asset tracing investigations
Our team of specialist forensic accountants and investigators have extensive experience in tracing assets and the flow of funds.
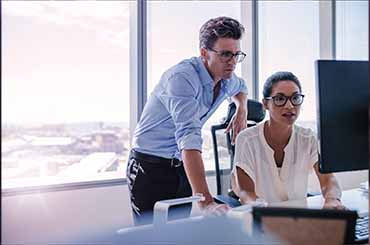
-
Mergers and acquisitions
Our mergers and acquisitions specialists guide you through the whole process to get the deal done and lay the groundwork for long-term success.
-
Acquisition search & strategy
We help clients identify, finance, perform due diligence and execute acquisitions to maximise the growth opportunities of your business.
-
Selling a business
Our M&A team works with clients to achieve a full or partial sale of their business, to ensure achievement of strategic ambitions and optimal outcomes for stakeholders.
-
Operational deal services
Our operational deal services team helps to ensure the greatest possible outcome and value is gained through post merger integration or post acquisition integration.
-
Transaction advisory
Our transaction advisory services support our clients to make informed investment decisions through robust financial due diligence.
-
Business valuations
We use our expertise and unique and in-depth methodology to undertake business valuations to help clients meet strategic goals.
-
Tax in mergers & acquisition
We provide expert advice for all M&A taxation aspects to ensure you meet all obligations and are optimally positioned.
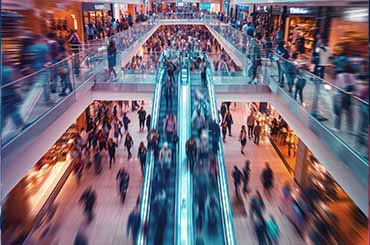
-
Corporate finance
We provide effective and strategic corporate finance services across all stages of investments and transactions so clients can better manage costs and maximise returns.
-
Debt advisory
We work closely with clients and lenders to provide holistic debt advisory services so you can raise or manage existing debt to meet your strategic goals.
-
Working capital optimisation
Our proven methodology identifies opportunities to improve your processes and optimise working capital, and we work with to implement changes and monitor their effectiveness.
-
Capital markets
Our team has significant experience in capital markets and helps across every phase of the IPO process.
-
Debt and project finance raising
Backed by our experience accessing full range of available funding types, we work with clients to develop and implement capital raising strategies.
-
Private equity
We provide advice in accessing private equity capital.
-
Financial modelling
Our financial modelling advisory team provides strategic, economic, financial and valuation advice for project types and sizes.
-
Payments advisory
We provide merchants-focused payments advice on all aspects of payment processes and technologies.
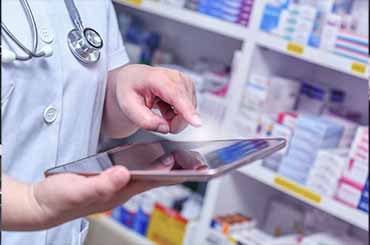
-
Voluntary administration & DOCA
We help businesses considering or in voluntary administration to achieve best possible outcomes.
-
Corporate insolvency & liquidation
We help clients facing corporate insolvency to undertake the liquidation process to achieve a fair and orderly company wind up.
-
Complex and international insolvency
As corporate finance specialists, Grant Thornton can help you with raising equity, listings, corporate structuring and compliance.
-
Safe Harbour advisory
Our Safe Harbour Advisory helps directors address requirements for Safe Harbour protection and business turnaround.
-
Bankruptcy and personal insolvency
We help clients make informed choices around bankruptcy and personal insolvency to ensure the best personal and stakeholder outcome.
-
Creditor advisory services
Our credit advisory services team works provides clients with credit management assistance and credit advice to recapture otherwise lost value.
-
Small business restructuring process
We provide expert advice and guidance for businesses that may need to enter or are currently in small business restructuring process.
-
Asset tracing investigations
Our team of specialist forensic accountants and investigators have extensive experience in tracing assets and the flow of funds.
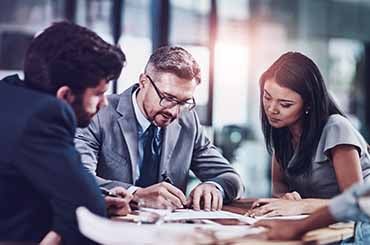
-
Independent business reviews
Does your company need a health check? Grant Thornton’s expert team can help you get to the heart of your issues to drive sustainable growth.
-
Commercial performance
We help clients improve commercial performance, profitability and address challenges after internal or external triggers require a major business model shift.
-
Safe Harbour advisory
Our Safe Harbour advisory helps directors address requirements for Safe Harbour protection and business turnaround.
-
Corporate simplification
We provide corporate simplification and managed wind-down advice to help streamline and further improve your business.
-
Director advisory services
We provide strategic director advisory services in times of business distress to help directors navigate issues and protect their company and themselves from liability.
-
Debt advisory
We work closely with clients and lenders to provide holistic debt advisory services so you can raise or manage existing debt to meet your strategic goals.
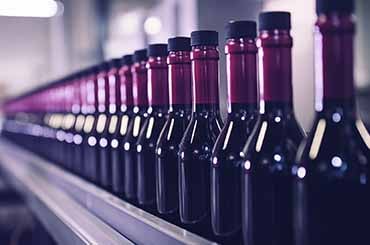
-
Business planning & strategy
Our clients can access business planning and strategy advice through our value add business strategy sessions.
-
Private business company secretarial services
We provide company secretarial services and expert advice for private businesses on all company secretarial matters.
-
Outsourced accounting services
We act as a third-party partner to international businesses looking to invest in Australia on your day-to-day finance and accounting needs.
-
Superannuation and SMSF
We provide SMSF advisory services across all aspects of superannuation and associated tax laws to help you protect and grow your wealth.
-
Management reporting
We help you build comprehensive management reporting so that you have key insights as your business grows and changes.
-
Financial reporting
We help with all financial reporting needs, including set up, scaling up, spotting issues and improving efficiency.
-
Forecasting & budgeting
We help you build and maintain a business forecasting and budgeting model for ongoing insights about your business.
-
ATO audit support
Our team of experts provide ATO audit support across the whole process to ensure ATO requirements are met.
-
Family business consulting
Our family business consulting team works with family businesses on running their businesses for continued future success.
-
Private business taxation and structuring
We help private business leaders efficiently structure their organisation for optimal operation and tax compliance.
-
Outsourced CFO services
Our outsourced CFO services provide a full suite of CFO, tax and finance services and advice to help clients manage risk, optimise operations and grow.
-
ESG & sustainability reporting
There is a growing demand for organisations to provide transparency on their commitment to sustainability and disclosure of the nonfinancial impacts of their business activities. Commonly, the responsibility for sustainability and ESG reporting is landing with CFOs and finance teams, requiring a reassessment of a range of reporting processes and controls.
-
ESG & sustainability advisory
With the ESG and sustainability landscape continuing to evolve, we are focussed on helping your business to understand what ESG and sustainability represents and the opportunities and challenges it can provide.
-
ESG, sustainability and climate reporting assurance
As the demand for organisations to prepare information in relation to ESG & sustainability continues to increase, through changes in regulatory requirements or stakeholder expectations, there is a growing need for assurance over the information prepared.
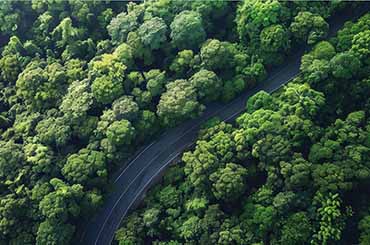
-
Management consulting
Our management consulting services team helps you to plan and implement the right strategy to deliver sustainable growth.
-
Financial consulting
We provide financial consulting services to keep your business running so you focus on your clients and reaching strategic goals.
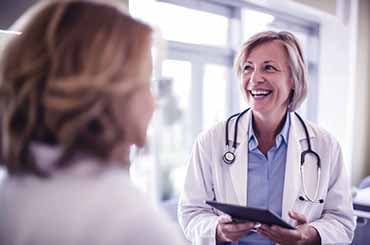
-
China practice
The investment opportunities between Australia and China are well established yet, in recent years, have also diversified.
-
Japan practice
The trading partnership between Japan and Australia is long-standing and increasingly important to both countries’ economies.
-
India practice
It’s an exciting time for Indian and Australian businesses looking to each jurisdiction as part of their growth ambitions.
-
Singapore practice
Our Singapore Practice works alongside Singaporean companies to achieve growth through investment and market expansion into Australia.
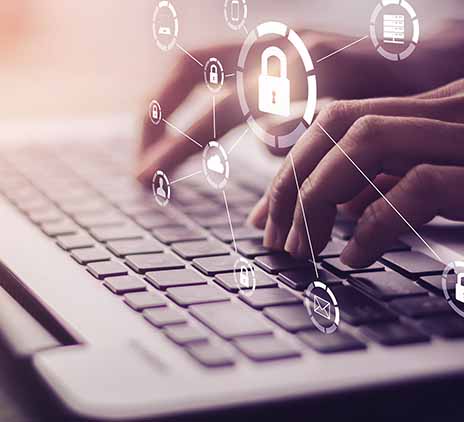
-
Insight Australian wine export strategies post-China tariff removalFollowing the recent removal of tariffs on Australian wine by China, the industry is keen to rebuild relations and explore the right export markets. This presents Australian wine producers with a chance to reassess their position in the global market.
-
Insight Identify your opportunities in the complex landscape of fuel tax creditsThe landscape of fuel tax credits (FTC) is constantly evolving due to ongoing economic and technological developments. This dynamic environment presents both challenges and opportunities for businesses with significant fuel consumption.
-
Client Alert March 2024 Update: NSW Grants for Net Zero Manufacturing and Physical SciencesSome major NSW grant programs have been announced, supporting projects in clean technology innovation, low carbon product manufacturing, renewable manufacturing and physical sciences.
-
Insight Navigating a complex Agribusiness, Food and Beverage deals landscape in 2024Despite a 14% global decline in Agribusiness, Food, and Beverage M&A deals, 2024 shows promise with expected global interest rate stabilisation. Given the sector's role in global sustainability, businesses can tap into opportunities in food manufacturing and waste minimisation.
-
Renewable Energy
Transformation through energy transition
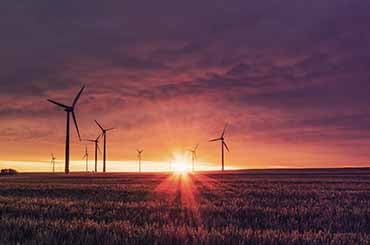
-
Business Planning and Strategy
Having an honest, broad-reaching and thought-provoking discussion with a skilled, independent advisor can be the catalyst for clarity – a direction to take your business forward and an understanding of what is key to success.
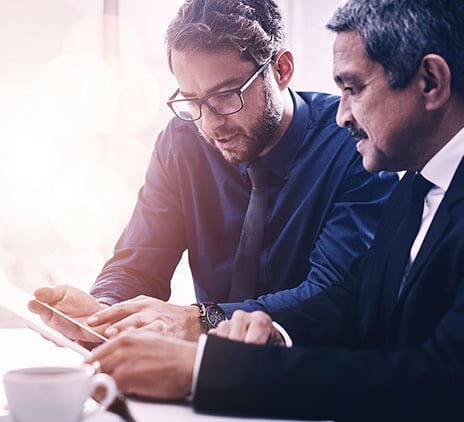
-
Flexibility & benefits
The compelling client experience we’re passionate about creating at Grant Thornton can only be achieved through our people. We’ll encourage you to influence how, when and where you work, and take control of your time.
-
Your career development
At Grant Thornton, we strive to create a culture of continuous learning and growth. Throughout every stage of your career, you’ll to be encouraged and supported to seize opportunities and reach your full potential.
-
Diversity & inclusion
To be able to reach your remarkable, we understand that you need to feel connected and respected as your authentic self – so we listen and strive for deeper understanding of what belonging means.
-
In the community
We’re passionate about making a difference in our communities. Through our sustainability and community engagement initiatives, we aim to contribute to society by creating lasting benefits that empower others to thrive.
-
Graduate opportunities
As a new graduate, we aim to provide you more than just your ‘traditional’ graduate program; instead we kick start your career as an Associate and support you to turn theory into practice.
-
Vacation program
Our vacation experience program will give you the opportunity to begin your career well before you finish your degree.
-
The application process
Applying is simple! Find out more about each stage of the recruitment process here.
-
FAQs
Got questions about applying? Explore frequently asked questions about our early careers programs.
-
Our services lines
Learn about our services at Grant Thornton
-
Current opportunities
Current opportunities
-
Remarkable people
Our team members share their remarkable career journeys and experiences of working at Grant Thornton.
-
Working at Grant Thornton
Explore our culture, benefits and ways we support you in your career.
-
Current opportunities
Positions available.
-
Contact us
Get in touch
It’s becoming a familiar tale: business disrupts the normal and expected; business reaps rewards.
Today’s global environment is marked by uncertainty, complexity and swift change. Businesses that have shaken-up their industries, either through innovative products and services or by streamlining systems and processes are proving to be the winners. Driving this creative storm is technology. A recent Grant Thornton survey shows a clear correlation between accelerated growth for mid-size businesses and the smart use of technology in a range of sectors.
So, how is technology shaping the future of the construction industry? And how can you transition from disrupted to disruptor?
Every part of our economy is being changed by technology’s disruptive influence. While some businesses are capitalising on it; some are at risk of being left behind. The real estate and construction industry is responsible for shaping the cities we live in and designing the places in which we work, live and play and therefore should be the vanguard of this disruption. As the Australian economy transitions away from the mining boom, businesses in the construction sector are seeking efficiencies to give them an edge. The Federal Government is supporting this mindset not least with its ‘Innovation Statement’, unveiled in December 2015. With almost $1.1 billion pledged over the next four years to promote business-based research, development and innovation, the Innovation package could provide an important springboard for mid-size businesses embracing technology. With 40 million citizens projected to call Australia home by 2055 1, innovation will be critical to the way we construct the homes and business places of the future to ensure access for all demographics.
Much of the innovation and new technology developed globally in the real estate and construction industry has been centered on sustainability. New materials, 3D printing, pre-fabrication, and modular approaches are among the emerging trends shaking up the construction industry and boosting growth for those who are ready to adopt, particularly in Australia where take up has been slow to date. Agile, mid-size businesses in the construction industry are well placed to take this next step in local innovation and capitalise on the growth opportunities on offer.
Modular construction
Modular construction is a growing trend and being picked up by a number of Australian businesses, some out of necessity. To enhance efficiency, some Not for Profit organisations (among others) have adopted this technology in the construction of aged care facilities, with successful outcomes reported of minimized construction times and wastage and a higher focus on quality, optimising their limited resources to achieve the organisation’s objectives.
Chinese company, Broad Sustainable Building Co Ltd (BSB), used the modular approach to build the world’s tallest pre-fabricated building in central China. Standing at 57 storeys the building’s construction was completed in just 19 days – a remarkable rate of three floors per day! The company realised many benefits including cost savings with less risk of lost days and reduced holding costs, and a minimised impact on the surrounding environment.
Pre-fabrication
Some of the big, global players in the construction sector are leading the way locally in disrupting through adopting technology in construction processes. LendLease has embraced pre-fabrication technology to change the way their building materials are produced over the next five years. The company has invested $15 million to start up pre-fabrication operation Design Make in western Sydney, creating up to 70 construction and design jobs in the process. The company expects to realise significant benefits by limiting waste, reducing transport costs, and the time it takes to construct on-site.
The benefits of prefabrication 2 include:
- Up to 90% faster construction
- 100% re-use of componentry
- Reduction in site waste by up to 80%
- Reduce transport, labour, site preliminaries by 70%
Innovative materials
A huge amount of research is being undertaken globally on any given day to improve the longevity and safety of the materials used in the construction of our cities and our homes. From the development of self-healing concrete that is being tested by the University of Cardiff, that could have a massive impact on the sustainability of our infrastructure (think tunnels, bridges and buildings) through to heat reflective paint that could reduce cooling needs and the maintenance on our homes. While the rest of the world has picked up on the use of timber framing in high rise buildings, the National Construction Code in Australia has only recently been updated to allow for structures (up to 8 storeys). So while there may be businesses willing to utilise the innovative materials being developed, our regulatory codes need to keep abreast of the changes and allow for the technology to be embraced.
What can you do now to take your business from disrupted to disruptor?
It’s no longer an option to leave technology choices solely to the IT department or innovation to an R&D team. Strategic approaches at board level are necessary for businesses to capitalise on their investment in technology and realise the efficiency and productivity returns sought. With technology critical to future growth, boards and C-suite executives must lead their business’ digital transformation across the organisation, rather than rely on their IT department to lead innovation piecemeal.
Companies need to have a clear strategy that identifies where the biggest difference can be made with technology, and align business goals and technology requirements with choices that are guided by a customer-centric approach rather than a technical checklist. For those willing to embrace technology there is significant growth on offer – and some of the best in the business are gearing up to transform their businesses through technology. For those who prefer to wait and see how their early adopting competitors fare when implementing technology currently available, change will become necessary if they are to remain competitive. If competitors are able to benefit from enhanced processes and efficiency, the adoption of innovative technology in the construction industry will not be a “nice to have”, it will be a necessity to compete and grow.
The upside of adopting technology
- faster construction times
- reduced labour costs
- fewer defects
- less waste
- better health and safety, and
- better productivity from existing resources
The last point is particularly attractive for businesses and lenders alike. The broader community also benefits from sustainable construction practices and materials.
Consider the risks when adopting technology
With innovation comes risk. Those looking at pre-fabrication should consider upfront the difficulties involved in customisation and changes to specifications for their products and the knock-on effect to projects. The slow adoption of technology presents risks of its own: the limited understanding of new construction practices by the broader public could expose businesses to negative perceptions of quality and value. It is vital that those who adopt technology as part of their growth strategy are forefront in educating the business community, financiers and consumers of the benefits so the new practices become mainstream sooner.
If the Australian construction industry is to compete and encourage growth in local and global markets, investment in technology is a must. Internationally, construction businesses are already taking this step, and much can be learned from their experience. Businesses that embrace technology to improve their processes will play a leading role in keeping up with the demand of Australia’s growing population, and reap efficiency and profitability benefits in the process.
[1] 2015 Intergenerational Report
[2] ARC training centre for advanced manufacturing of prefabricated housing